Lean Six Sigma Certification Training FAQs
Why we're the go to training provider for you
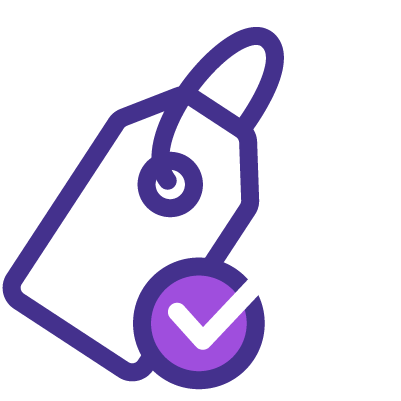
Best price in the industry
You won't find better value in the marketplace. If you do find a lower price, we will beat it.
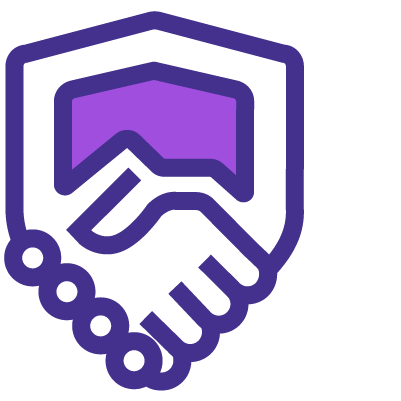
Trusted & Approved
We are accredited by PeopleCert on behalf of AXELOS
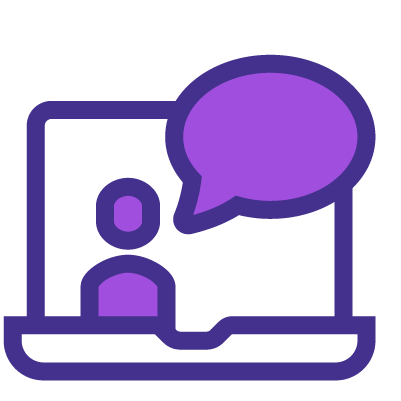
Many delivery methods
Flexible delivery methods are available depending on your learning style.
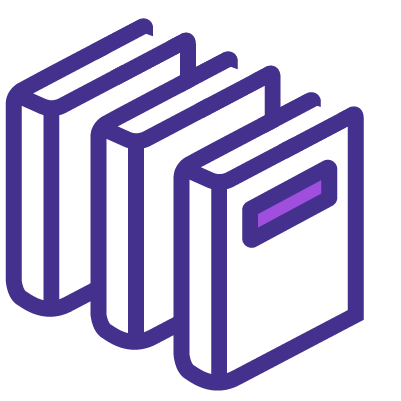
High quality resources
Resources are included for a comprehensive learning experience.
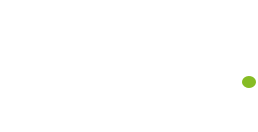

"Really good course and well organised. Trainer was great with a sense of humour - his experience allowed a free flowing course, structured to help you gain as much information & relevant experience whilst helping prepare you for the exam"
Joshua Davies, Thames Water
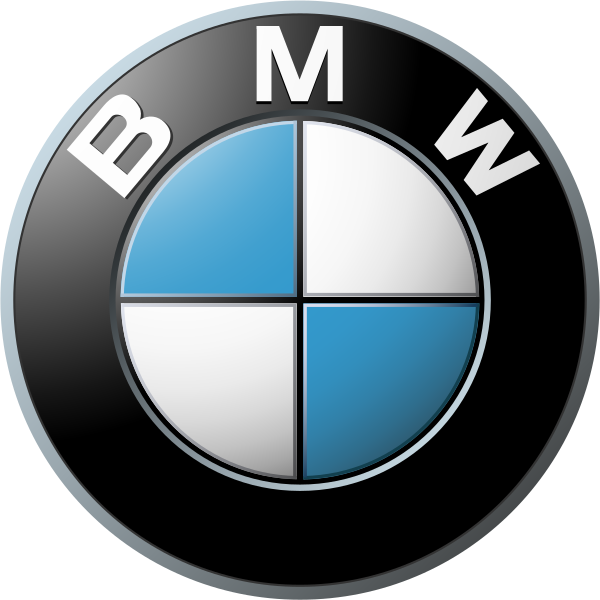
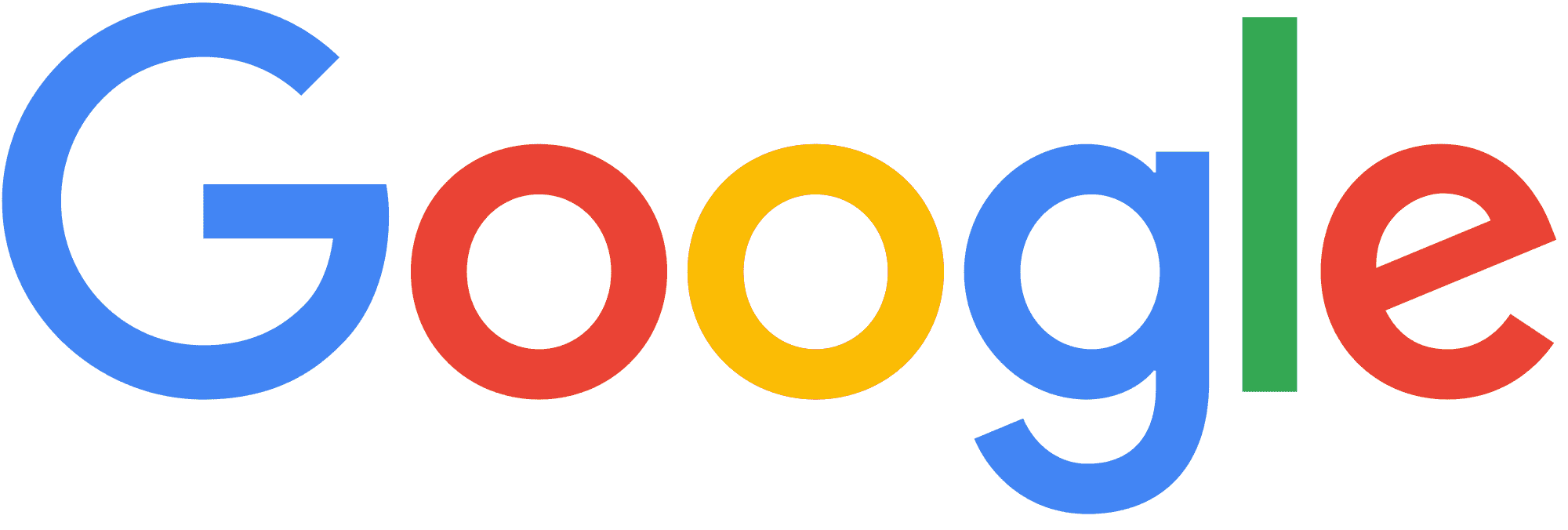