We may not have the course you’re looking for. If you enquire or give us a call on 01344203999 and speak to our training experts, we may still be able to help with your training requirements.
Training Outcomes Within Your Budget!
We ensure quality, budget-alignment, and timely delivery by our expert instructors.
Organisations often adopt international standards like ISO 45001 to establish a safe and healthy workplace. It is an internationally recognised Occupational Health and Safety (OH&S) Management Standard developed by International Organization for Standardization (ISO). ISO 45001 Implementation can be daunting as you need to fulfil requirements, conduct audits and continually improve on it.
According to the International Labour Organization, about 2.3 million employees face work-related accidents or diseases every year. This is an alarming trend, and incidents like these can be reduced significantly by implementing safety standards like ISO 45001. Read this blog to learn all there is to know about ISO 45001 Implementation and tips for implementing it in the workplace.
Table of Contents
1) What is ISO 45001?
2) Detailed guide of ISO 45001 Implementation
3) Implementing the ISO 45001 requirements
4) Tips on how to implement ISO 45001
5) Conclusion
What is ISO 45001?
ISO 45001 is a globally recognised OH&S Management System standard providing a framework to systematically manage occupational health and safety risks and opportunities, promoting a safe work environment for employees and stakeholders.
ISO 45001 aims to improve an organisation's overall health and safety performance by enabling effective hazard identification, risk assessment, and risk control measures. By implementing ISO 45001, organisations can demonstrate their commitment to employee well-being, legal compliance, and continuous improvement in occupational health and safety management.
Detailed guide of ISO 45001 Implementation
Even if your organisation doesn't plan to get the ISO 45001 Certification, implementing it can benefit your organisation in various ways. If you are wondering how to implement ISO 45001, here's a detailed implementation guideline.
Commitment from the leadership and management
Leadership commitment is crucial for ISO 45001 Implementation. It involves setting clear objectives, allocating resources, integrating safety into the organisational culture, leading by example, communicating effectively, and participating in the review process. When leaders prioritise health and safety, it creates a culture where everyone takes responsibility for safety and actively contributes to its improvement.
Establishing an implementation team
Establishing a diverse and engaged implementation team is vital for successfully implementing ISO 45001. The team must involve representatives from different departments, ensuring a cross-functional approach. Leadership involvement is crucial to provide guidance and allocate resources.
Effective communication and collaboration within the team facilitate the flow of information and promote a sense of ownership. Clear roles and responsibilities for team members ensure comprehensive coverage of ISO 45001 requirements. Regular meetings allow for progress updates and issue resolution. Organisations can streamline the implementation process and foster a safer work environment by establishing such a team.
Conducting gap analysis
Conducting a gap analysis is a necessary step in implementing ISO 45001 Implementation. This process involves carefully reviewing the organisation's current occupational health and safety practices, policies, and procedures and comparing them against the requirements outlined in the ISO 45001 Standard. By doing so, any gaps or areas of non-compliance can be identified and addressed.
During the gap analysis, it is essential to conduct Evaluation of Compliance of ISO 45001 for an organisation's level of compliance with relevant legal and regulatory requirements of occupational health and safety. This includes reviewing documentation, permits, licenses, and records to ensure adherence to legal obligations. Any areas of non-compliance should be highlighted and incorporated into the action plan.
Once the gaps have been identified, it is essential to prioritise them based on their significance and potential impact on occupational health and safety. This allows for the effective allocation of resources and efforts during the implementation process.
Enhance your organisation's Occupational Health and Safety Management System with our comprehensive ISO 45001 Foundation training today!
Develop an implementation plan
Developing a comprehensive implementation plan is crucial for successfully implementing ISO 45001. Consider the organisational context and set clear objectives and targets aligned with the organisation's goals. Allocate necessary resources and establish clear roles and responsibilities.
Develop policies and procedures that align with ISO 45001 requirements and implement effective communication and training programs. Establish controls and monitoring mechanisms to ensure compliance and enable continuous improvement. By developing a well-structured and detailed plan, organisations can effectively navigate the implementation process, allocate resources, clarify responsibilities, and establish processes for ongoing improvement.
Risk assessment and controls
Risk assessment and control are essential components of ISO 45001 Implementation. This process involves systematically identifying, evaluating, and managing risks to prevent workplace accidents, injuries, and illnesses.
Identifying the potential hazards at the workplace is the first step in risk assessment. This includes physical hazards (e.g., machinery, chemicals), ergonomic hazards (e.g., poor workstation setup), psychosocial hazards (e.g., work-related stress), and any other factors that may pose a threat to the health and safety of employees.
Once hazards are identified, their associated risks are assessed and evaluated for the likelihood and potential severity of harm from exposure to each hazard. Risk assessment methods, such as risk matrices or qualitative assessments, can be used to determine the level of risk for each identified hazard.
After assessing the risks, control measures are implemented to eliminate or minimise them. The hierarchy of controls, as outlined by ISO 45001, should be followed:
a) Elimination: If feasible, hazards should be eliminated from the workplace. This may involve substituting hazardous materials or processes with safer alternatives.
b) Substitution: If elimination is impossible, hazardous materials or processes should be replaced with less hazardous ones.
c) Engineering controls: Physical modifications, such as installing machine guards or improving ventilation systems, can be implemented to reduce exposure to hazards.
d) Administrative controls: Policies, procedures, and work practices can be established to reduce the likelihood of exposure to hazards. This may include implementing training programs, establishing safe work procedures, and providing clear signage and instructions.
e) Personal Protective Equipment (PPE): When all other control measures are insufficient, PPE, such as helmets, gloves, or respirators, should be provided and used to protect employees from identified risks.
Regular reviews and reassessments of control measures are necessary to ensure their effectiveness. Any changes in the workplace, such as new processes or equipment, should trigger a reassessment of risks and appropriate adjustment of control measures.
Organisations can significantly reduce the likelihood and severity of workplace accidents and illnesses by conducting thorough risk assessments and implementing effective control measures. This proactive approach demonstrates a commitment to employee safety and aligns with the ISO 45001 Standard's requirements.
Learn all about the ISO 45001 Standard and improve your workplace's health and safety standards with our comprehensive ISO 45001 Certification today
Documentation and procedures
Effective documentation and procedures are crucial for the successful implementation of ISO 45001. The Occupational Health and Safety Manual serves as a foundation, outlining the organisation's commitment to the standard and providing an overview of the Occupational Health and Safety Management System. Standard Operating Procedures (SOPs) are essential, detailing processes for hazard identification, risk assessment, incident reporting, emergency response, and personal protective equipment.
Risk assessment and control procedures should outline the steps for identifying hazards, evaluating risks, and implementing appropriate controls. Incident reporting and investigation procedures help ensure timely reporting, thorough investigations, and the implementation of corrective actions. An emergency response plan establishes guidelines for emergencies and facilitates effective coordination.
By developing concise and clear documentation and procedures, organisations provide a framework for employees to understand their responsibilities and contribute to maintaining a safe working environment, aligning with ISO 45001 requirements and facilitating continuous improvement.
Training and awareness
Training and awareness empower employees with the necessary knowledge and skills to ensure a safe work environment. Conduct a thorough training needs assessment to identify specific requirements. Develop a comprehensive program covering hazard identification, risk assessment, emergency procedures, PPE use, and legal compliance. Use suitable delivery methods and encourage employee engagement to foster a supportive learning environment.
Provide ongoing training and refresher courses to reinforce knowledge and address updates. Complement training with awareness campaigns using various communication channels. Continuously evaluate and gather feedback to improve training effectiveness. By prioritising training and awareness, organisations empower employees to identify hazards, promote a safety culture, and successfully implement ISO 45001.
Internal audits and management reviews
When conducted regularly, internal audits assess compliance with ISO 45001 requirements, identify areas for improvement, and serve as a basis for corrective actions. Management reviews, held at planned intervals, evaluate the system's performance, review incident data, performance indicators, and compliance, and set new objectives for improvement.
Proper documentation and reporting of audit findings, review outcomes, and corrective actions ensure transparency and accountability. The goal is to establish a proactive safety culture that prioritises employee well-being and aligns with ISO 45001 principles. Internal audits and management reviews create a feedback loop for informed decision-making, resource allocation, and constant enhancement.
Learn how to effectively carry out internal audits and assess company compliance with ISO 45001 Internal Auditor training.
Implementing the ISO 45001 requirements
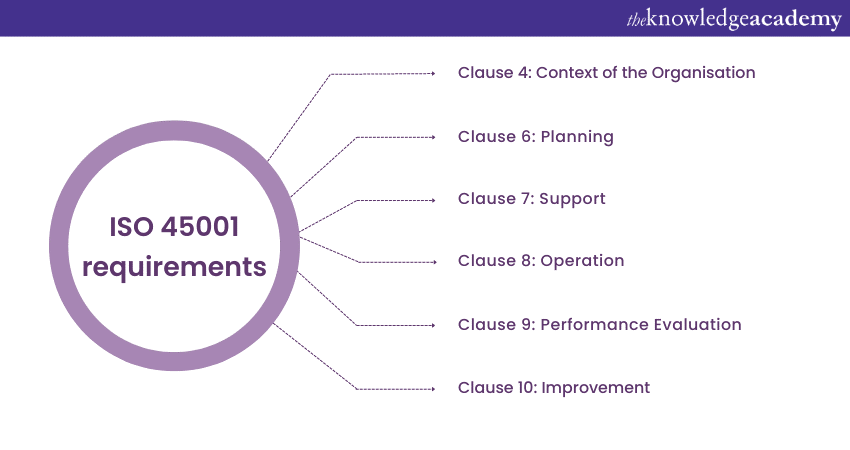
The essence of ISO 45001 Implementation depends on how well you follow or fulfil the requirements detailed in the standard. Organisations can systematically implement the ISO 45001 Requirements by following these steps for each clause.
a) Clause 4: Context of the organisation
a) Identify and understand the factors affecting occupational health and safety.
b) Determine the needs and expectations of relevant interested parties.
c) Document and maintain this information for reference and decision-making.
d) Top management should demonstrate leadership commitment to occupational health and safety.
e) Establish clear roles, responsibilities, and authorities for all levels of the organisation.
f) Encourage worker participation and consultation in health and safety matters.
b) Clause 6: Planning
a) Set measurable objectives and targets for improving occupational health and safety.
b) Develop action plans to achieve these objectives, including allocating necessary resources.
c) Conduct hazard identification and risk assessment to address potential hazards and risks.
c) Clause 7: Support
a) Provide resources, such as training, tools, and infrastructure, to effectively implement the occupational health and safety management system.
b) Ensure workers have access to relevant information, including policies, procedures, and legal requirements.
c) Establish communication channels to facilitate internal and external communication on health and safety matters.
d) Clause 8: Operation
a) Implement procedures for hazard identification, risk assessment, incident reporting, and emergency preparedness.
b) Establish controls and safeguards to minimise risks and prevent incidents.
c) Promote safe work practices and effectively use Personal Protective Equipment (PPE).
e) Clause 9: Performance Evaluation
a) Monitor and measure the performance of the Occupational Health and Safety Management system against objectives and targets.
b) Conduct regular internal audits to assess compliance and identify areas for improvement.
c) Analyse incident data, performance indicators, and feedback to evaluate system effectiveness.
f) Clause 10: Improvement
a) Take corrective actions to address identified non-conformities and improve the system's effectiveness.
b) Continually seek opportunities for improvement, such as enhancing controls, training programs, and communication processes.
c) Review the effectiveness of the Occupational Health and Safety Management system and make necessary adjustments.
Become a certified Lead Auditor and improve your organisation's Occupational Health and Safety Management System with ISO 45001 Lead Auditor training.
Tips on how to implement ISO 45001
Implementing ISO 45001 can be a complex process, but here are some tips to help you navigate through it successfully:
1) Gain leadership support: Obtaining the commitment and support of top management is crucial for the successful implementation of ISO 45001. They should actively participate and demonstrate their dedication to occupational health and safety.
2) Involve employees: Engage employees at all levels throughout the implementation process. Seek their input, involve them in risk assessments, and provide adequate training to ensure their active participation and ownership of the system.
3) Seek external expertise: Consider engaging external consultants or experts with experience in ISO 45001 Implementation. They can provide valuable guidance, assist in conducting a thorough gap analysis, and help develop an effective implementation plan.
4) Continual improvement: ISO 45001 emphasises the importance of continuous improvement. Encourage a learning culture where employees are encouraged to report hazards and incidents and suggest improvements.
Conclusion
ISO 45001 Implementation is a strategic decision demonstrating an organisation's commitment to the health and safety of its employees. By following the steps outlined in this guide and incorporating the tips provided, organisations can establish a robust OH&S management system that aligns with ISO 45001 requirements. The journey towards ISO 45001 compliance may require effort and resources, but the benefits of a safer and healthier workplace are invaluable for both employees and the organisation.
Become a Lead Implementer and help your organisation achieve and maintain compliance with our ISO 45001 Lead Implementer Training.
Frequently Asked Questions
There are five steps which can help you to implement ISO 45001 in the workplace. These are as follows:
a) You need to understand the Occupational Safety and Health management Systems and ISO 45001
b) You have to properly examine your current system
c) Then, engage with the stakeholders of your organisation
d) Your company’s goals and priorities have to be determined
e) You have to improve your OSH Management System
If an organisation has equal to or less than 20 people, then the implementation of ISO 45001 would take approximately six months. However, it will also depend on the focus, knowledge, resource available and expertise of those people in that organisation.
The Knowledge Academy’s Knowledge Pass, a prepaid voucher, adds another layer of flexibility, allowing course bookings over a 12-month period. Join us on a journey where education knows no bounds.
Discover ISO Certification courses with The Knowledge Academy, offering ISO 56002 Innovation Management System Training, ISO 10218-1 Robots and Robotic Devices Training, and ISO 20121 Event Sustainability Management System Training. Designed for diverse skill levels, these courses provide a comprehensive understanding of ISO 9001 Internal Audit.
Whether you are starting your journey or aiming to elevate your ISO and Compliance expertise, immerse yourself in our ISO and Compliance blogs to discover more insights!
The Knowledge Academy takes global learning to new heights, offering over 30,000 online courses across 490+ locations in 220 countries. This expansive reach ensures accessibility and convenience for learners worldwide.
Alongside our diverse Online Course Catalogue, encompassing 17 major categories, we go the extra mile by providing a plethora of free educational Online Resources like News updates, Blogs, videos, webinars, and interview questions. Tailoring learning experiences further, professionals can maximise value with customisable Course Bundles of TKA.
Upcoming Health & Safety Resources Batches & Dates
Date
Mon 20th May 2024
Mon 22nd Jul 2024
Mon 23rd Sep 2024
Mon 11th Nov 2024